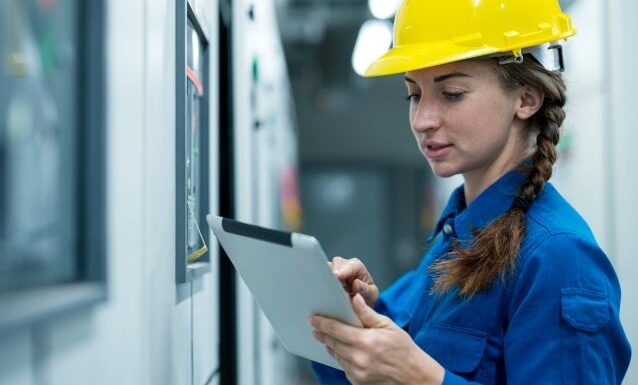
There are several benefits to preventative maintenance in the workplace. These programs can be time-based, predictive, or IoT-based. To get started, designate a few goals for your company, and include them in a spreadsheet. The next step is to schedule preventative maintenace to reduce energy costs in advance. Then choose a convenient day that won’t disrupt productivity.
Predictive maintenance
Predictive maintenance is a necessary process that can extend the life of the equipment. This process uses real-time data to predict when a component will fail and perform maintenance before it happens. It also prevents unplanned emergency work and increases the reliability of a production line. However, this process is expensive to implement and may require the services of highly trained employees.
It can also be used to manage buildings and energy costs. Preventative maintenace to reduce energy costs uses sensors to monitor equipment and assess its health. Artificial intelligence and predictive maintenance technology can inform energy industry companies when equipment is about to fail. Predictive maintenance is essential for manufacturing facilities, as they have many expensive assets. By compiling machine data, maintenance personnel can identify problems early on, saving them money in the long run.
Proactively monitoring equipment’s health and performing predictive maintenance can help businesses cut energy costs. Faulty equipment can consume a lot of energy each month, costing a fortune to replace. This can be done using advanced diagnostics such as ultrasound or vibration analysis. The goal is to identify problems before they become major and cost the company a lot of money. This prevents downtime and unexpected costs.
Time-based preventive maintenance
Time-based preventive maintenance is an essential strategy for organizations. It saves money and minimizes risks. In addition to lowering energy costs, it can also decrease workers’ compensation and lawsuits. Time-based preventive maintenance can be applied to various assets, including machinery, equipment, and systems.
When implementing preventative maintenace to reduce energy costs, it is essential to have a clearly defined goal for each task. Without clear goals, it can be challenging to evaluate the effectiveness of preventive maintenance activities properly. Furthermore, it can be challenging to create an effective plan without detailed records. If a team does not know the goals for a task, they may skip critical steps.
The key to time-based preventive maintenance is to know when to perform maintenance on critical and boundary assets. Using this strategy allows facility managers to prioritize maintenance tasks and schedule them at regular intervals, such as once every ten days or every three months. This proactive strategy also reduces budget uncertainty and extends the asset’s lifespan. As a result, time-based preventive maintenance can reduce energy costs.
IoT-based preventive maintenance
IoT-based preventive maintenance can help manufacturers reduce energy costs and improve operational effectiveness. For example, predictive maintenance can prevent refrigeration system failures, leading to food and medicine waste. And in the case of critical infrastructures such as roads, bridges, and railways, IoT can improve the safety of these systems.
Today, most equipment has sensors built-in to provide real-time information to industrial control systems. However, an even older kit can be retrofitted with these sensors. The data collected can be analyzed locally or transferred to a microcontroller or processor to provide a more detailed analysis. This type of preventive maintenance requires more sensors but is more cost-effective than reactive preventative maintenance.
One area where IoT technology has the most promise is in monitoring remote assets. The cost of downtime is high regardless of location, so watching these assets in real-time is crucial. However, the traditional method relies on sending technicians to the field to check equipment. With IoT solutions, companies can remotely monitor vital performance metrics and receive alerts if anything goes wrong.
Condition monitoring
Using continuous automated monitoring systems has become more affordable in the past decade and has widened its use across various industries. These systems leverage technologies such as the Industrial Internet of Things (IIoT) and Artificial Intelligence (AI), which provide real-time performance information. This data helps maintenance professionals detect potential problems before they occur and avoid costly downtime.
Predictive maintenance benefits businesses in several ways, including increased productivity, reduced energy costs, and longer equipment life. However, the upfront costs for these programs can be high. By utilizing packaged solutions, owners can reduce their costs by reducing the need for engineering implementation and support. These systems also improve KPIs, yield/quality, and safety. For example, one major petroleum company found that they saved 50{80f14e4c3041694c328af2addf899a70c8fe9d627a3ad806638cd3303d91e261} of their energy costs by implementing a preventative maintenance system using this technology.
Before implementing condition monitoring, organizations must be ready to embrace the technology. Various factors must be considered, including the current level of knowledge, the ability to upskill existing personnel, and the appetite for change. Furthermore, the cost of implementation and ongoing monitoring must be balanced against the savings.